Non Destructive Testing (NDT)
In the oil and gas industry, particularly in the new construction and maintenance stage, NDT (Non Descructive Test) is widely used and compulsary to check the integrity of the vessel, tank, piping and other equipment. Most widely used nowadays including RT (radiograpic), UT (ultrasonic), AE (accoustic emission), IR (Infra red), ET (electromagnetic).
NDT Methods

Acoustic Emission
When a solid material is stressed, imperfections within the material emit short bursts of energy called "emissions". In much the same manner as ultrasonic testing, these acoustic emissions can be detected by special receivers. The source of the "emissions" can be evaluated through study of their strength, rate, and location.
Eddy Current
In eddy current testing, one of several electromagnetic testing methods, electrical currents are generated in a conductive material by an induced magnetic field. Interruptions in the flow of the electric currents (eddy currents), which are caused by imperfections or changes in a material's conductive properties, will cause changes in the induced magnetic field. These changes when detected, indicate the presence of a change in the test object.
Leak Testing
A variety of techniques are used to detect and locate leaks in pressure containment parts and structures. Leaks can be detected by using electronic listening devices, pressure gage measurements, liquid and gas penetrant techniques, and/or a simple soap bubble test.
Liquid Penetrant
Liquid penetrant testing is probably the most widely used NDT method. The test object or material is coated with a visible or fluorescent dye solution. The excess dye is removed from the surface, and then a developer is applied. the developer acts like a blotter and draws penetrant out of imperfections which open to the surface. With visible dyes, the vivid color contrast between the penetrant and the developer makes the "bleedout' easy to see. With fluorescent dyes, and ultraviolet lamp is used to make the "bleedout" fluoresce brightly, thus allowing the imperfection to be seen readily.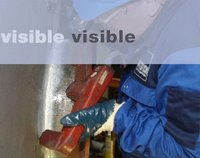
Magnetic Particle
Magnetic particle testing is done by inducing a magnetic field in a ferro-magnetic material and dusting the surface with iron particles (either dry or suspended in a liquid). Surface imperfections will distort the magnetic field and concentrate the iron particles near imperfections, thus indicating their presence.
Radiography
Radiography involves the use of penetrating X or gamma radiation to examine parts and products for imperfections. An X-ray machine or radioactive isotope is used as a source of radiation. Radiation is directed through a part and onto film. When the film is developed, a shadowgraph is obtained that shows the internal soundness of a part. Possible imperfections show up as density changes in the film, in much the same manner as an x-ray can show broken bones.
Ultrasonics
Ultrasonic testing uses the transmission of high frequency sound waves, into a material to detect imperfections within the material or changes in material properties. The most commonly used ultrasonic testing technique is pulse echo wherein sound is introduced into the test object and reflections (echoes) are returned to a receiver from interal imperfections or from geometrical surfaces of the part.
Visual Examination
Probably the oldest and most common method of NDT is visual examination, which has numerous industrial and commercial applications. Examiners follow procedures ranging from simple to very complex, some of which involve comparison of workmanship samples with production parts. Visual techniques are used wih all other NDT methods.
NDT Methods

Acoustic Emission
When a solid material is stressed, imperfections within the material emit short bursts of energy called "emissions". In much the same manner as ultrasonic testing, these acoustic emissions can be detected by special receivers. The source of the "emissions" can be evaluated through study of their strength, rate, and location.
Eddy Current
In eddy current testing, one of several electromagnetic testing methods, electrical currents are generated in a conductive material by an induced magnetic field. Interruptions in the flow of the electric currents (eddy currents), which are caused by imperfections or changes in a material's conductive properties, will cause changes in the induced magnetic field. These changes when detected, indicate the presence of a change in the test object.
Leak Testing
A variety of techniques are used to detect and locate leaks in pressure containment parts and structures. Leaks can be detected by using electronic listening devices, pressure gage measurements, liquid and gas penetrant techniques, and/or a simple soap bubble test.
Liquid Penetrant
Liquid penetrant testing is probably the most widely used NDT method. The test object or material is coated with a visible or fluorescent dye solution. The excess dye is removed from the surface, and then a developer is applied. the developer acts like a blotter and draws penetrant out of imperfections which open to the surface. With visible dyes, the vivid color contrast between the penetrant and the developer makes the "bleedout' easy to see. With fluorescent dyes, and ultraviolet lamp is used to make the "bleedout" fluoresce brightly, thus allowing the imperfection to be seen readily.
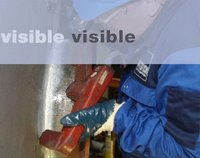
Magnetic Particle
Magnetic particle testing is done by inducing a magnetic field in a ferro-magnetic material and dusting the surface with iron particles (either dry or suspended in a liquid). Surface imperfections will distort the magnetic field and concentrate the iron particles near imperfections, thus indicating their presence.
Radiography
Radiography involves the use of penetrating X or gamma radiation to examine parts and products for imperfections. An X-ray machine or radioactive isotope is used as a source of radiation. Radiation is directed through a part and onto film. When the film is developed, a shadowgraph is obtained that shows the internal soundness of a part. Possible imperfections show up as density changes in the film, in much the same manner as an x-ray can show broken bones.
Ultrasonics
Ultrasonic testing uses the transmission of high frequency sound waves, into a material to detect imperfections within the material or changes in material properties. The most commonly used ultrasonic testing technique is pulse echo wherein sound is introduced into the test object and reflections (echoes) are returned to a receiver from interal imperfections or from geometrical surfaces of the part.
Visual Examination
Probably the oldest and most common method of NDT is visual examination, which has numerous industrial and commercial applications. Examiners follow procedures ranging from simple to very complex, some of which involve comparison of workmanship samples with production parts. Visual techniques are used wih all other NDT methods.
2 Comments:
Any enquiries on NDT, contact us http://www.opigroup.com
Any enquiries on NDT, contact us at http://www.opigroup.com
Post a Comment
<< Home